Инструкция по ремонту и замене деталей
Замена вышедшего из строя сервопривода
В процессе эксплуатации робота-манипулятора от чрезмерных нагрузок сервоприводы могут выходить из строя. В основном это происходит, если длительное время (до нескольких минут) удерживать “зажатыми” кнопки управления роботом-манипулятором. В таких случаях сервопривод перегревается и может выйти из строя.
Для замены вышедших из строя сервоприводов в комплект поставки включены запасные сервоприводы.
Расположение сервоприводов и их назначение представлены на рисунке.
Все сервоприводы подключаются к контактному разъему согласно схеме п. 4.2.
Внешний вид контактного разъема для подключения сервоприводов представлен на фото ниже:

Разъем №2: Сервопривод наклона стрелы (перемещение захвата вверх-вниз).
Разъем №3: Сервопривод наклона башни (перемещение захвата вперед-назад).
Разъем №4: Сервопривод захвата.
Разъем №5: Сервопривод поворота башни.
Для отключения сервопривода потяните за провода идущие к нужной вилке, чтобы вытащить ее из разъёма.
Для подключения сервопривода разверните разъем коричневым проводом к цифрам номера разъёма и вставьте вилку в разъем на корпусе до упора.
Замена сервопривода поворота башни
Шаг 1.
Отключите робота от компьютера и отключите его от блока питания. Аккуратно срежьте стяжки, которые фиксируют провод неисправного сервопривода, снимите оплетку со жгута проводов, чтобы освободить провод неисправного сервопривода.
Шаг 2.
Открутите с помощью крестовой отвертки два винта М3x35 чтобы отсоединить башню от основания. Придерживайте.
Шаг 3.
Открутите с помощью крестовой отвертки винт М2,5x6 фиксирующий малую шестерню основания башни на валу сервопривода. Снимите шестерню.
Шаг 4.
С помощью крестовой отвертки открутить шурупы М2х8, фиксирующие сервопривод и вытащить его из посадочного отверстия.
Шаг 5.
Отключите неисправный сервопривод от контактного разъема и уберите его. Достаньте из ложемента новый исправный сервопривод и установите его, соблюдая ту же последовательность как на предыдущем шаге.
Шаг 6.
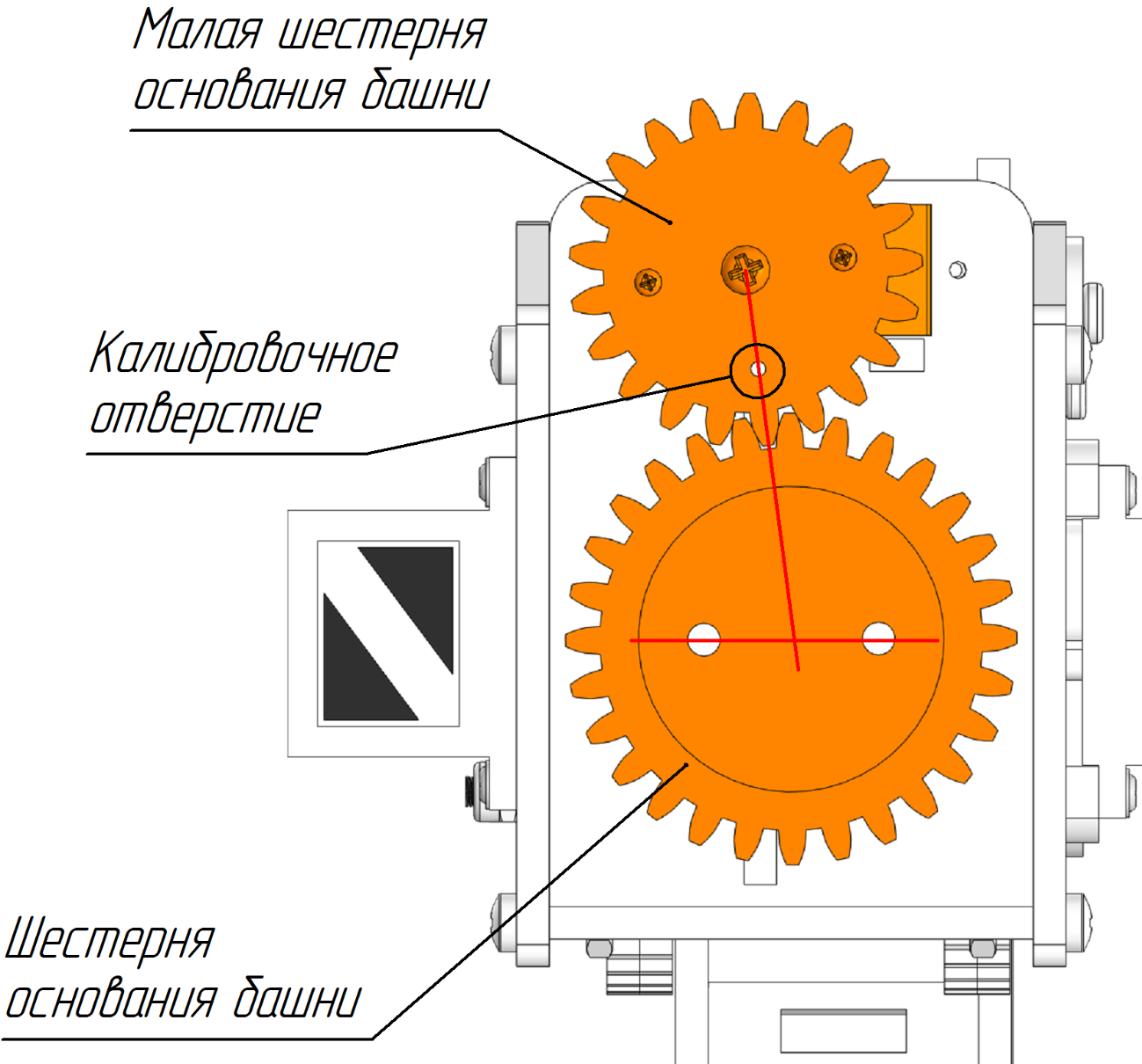
Шаг 7.
Закрепите малую шестерню сервопривода на валу сервопривода винтом М2,5x6. Установите башню на основание, закрутите винты М3x35.
Шаг 8.
Стяните жгут новыми стяжками, наденьте оплетку.
Замена сервоприводов перемещения захвата
Рассмотрим замену сервопривода перемещения захвата вперед-назад. Замена сервопривода перемещения захвата вверх-вниз производится аналогично.
Шаг 1.
Отключите робота от компьютера и отключите его от блока питания. Аккуратно срежьте стяжки, которые фиксируют провод неисправного сервопривода, снимите оплетку со жгута проводов, чтобы освободить провод неисправного сервопривода.
Шаг 2.
При помощи крестовой отвертки открутите два шурупа, которыми сервопривод крепится к стенке основания башни.
Шаг 3.
Снимите шестерню с неисправного сервопривода. Для этого, с помощью крестовой отвертки, открутите винт М2,5x6, фиксирующий малую шестерню на валу сервопривода.
Шаг 4.
Отключите неисправный сервопривод от контактного разъема и на его место подключите исправный сервопривод. Сервопривод подключается к соответствующему разъему (см. схему электрических соединений п. 4.2). При подключении соблюдать цветовую маркировку (см. фото - сверху вниз: коричневый, красный и желтый).
Шаг 5.
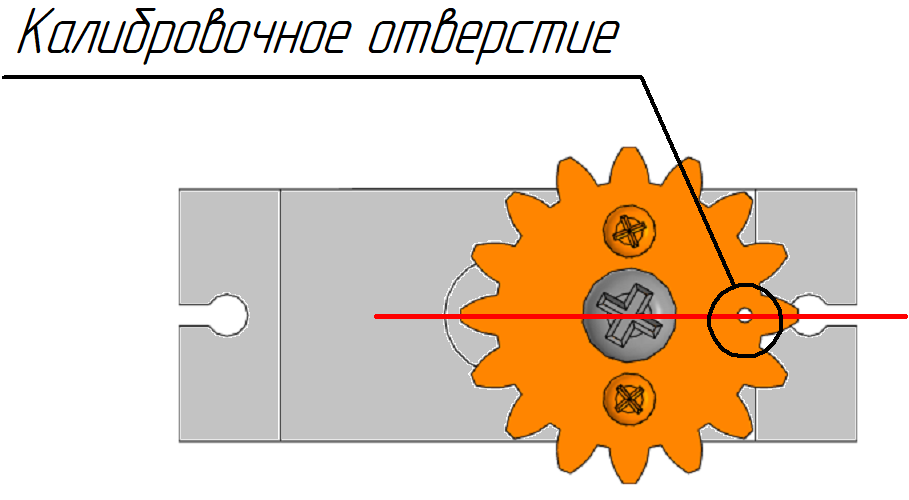
Шаг 6.
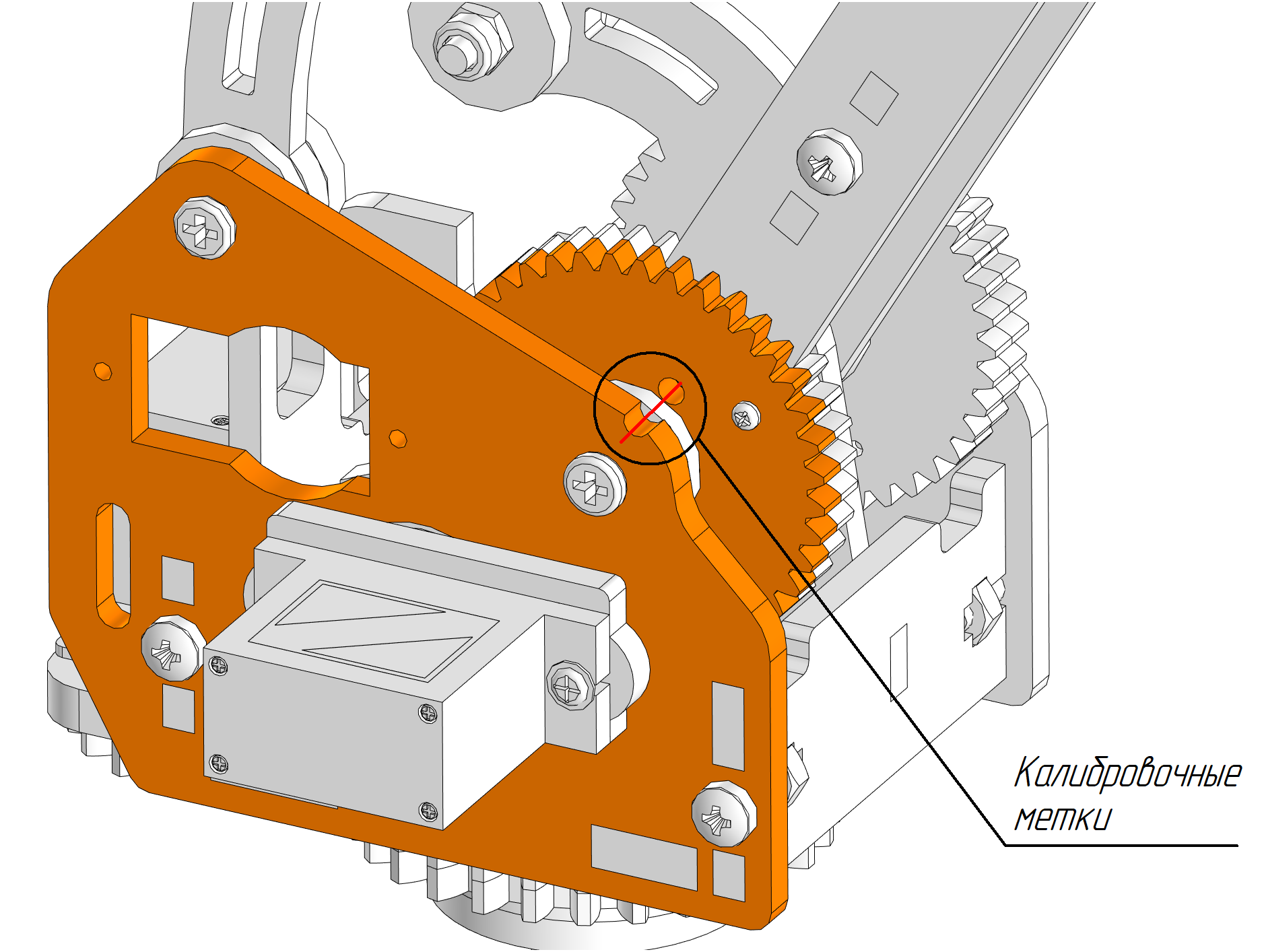
Шаг 7.
Стяните жгут новыми стяжками, наденьте оплетку.
Замена сервопривода захвата
Шаг 1.
Отключите робота от компьютера и отключите его от блока питания. Аккуратно срежьте стяжки, фиксирующие провод неисправного сервопривода.
Шаг 2.
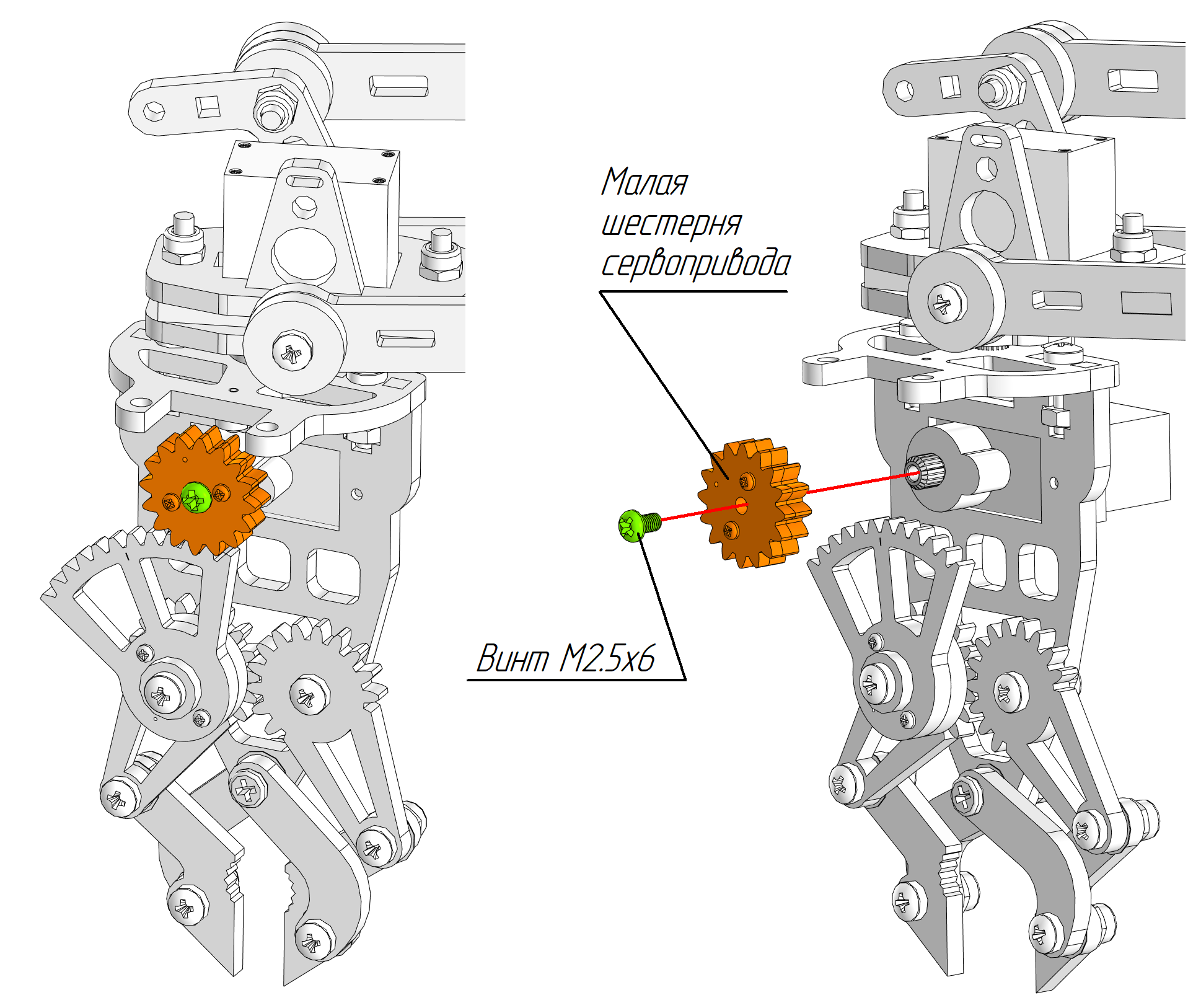
Шаг 3.
При помощи крестовой отвертки открутите два винта удерживающие сервопривод и снимите его.
Шаг 4.
Достаньте из ложемента новый исправный сервопривод и установите его, соблюдая ту же последовательность как на предыдущих шагах.
Шаг 5.
Подключите и уложите кабель сервопривода как показано на рисунке. Зафиксируйте провод стяжками идущими в комплекте запчастей.
Шаг 6.
Подключите к роботу блок питания. Подключите робота к компьютеру и запустите программу «Пульт управления РТУ». Установите сервопривод в среднее положение (см. раздел Позиционирование сервоприводов).
Шаг 7.
Не отключая питание робота, не закрывая окно программы «Пульт управления РТУ» и не закрывая окно выставки в среднее положение - установите малую шестерню сервопривода как показано на рисунке (метка на малой шестерни должна находиться слева, а метка на секторе привода-шестерни должна быть направлена вертикально вверх). После выставки, отключите робота от компьютера и его питание. Закройте окно «выставка в среднее положение» программы «Пульт управления РТУ». Закрутите винт удерживающий малую шестерню при помощи крестовой отвертки, слегка затяните (во время затяжки придерживайте шестерню пальцами не давая ей вращать вал сервопривода).
После выполнения всех шагов замена сервопривода завершена и робот готов к дальнейшей работе.
Замена сервопривода поворота захвата
Шаг 1.
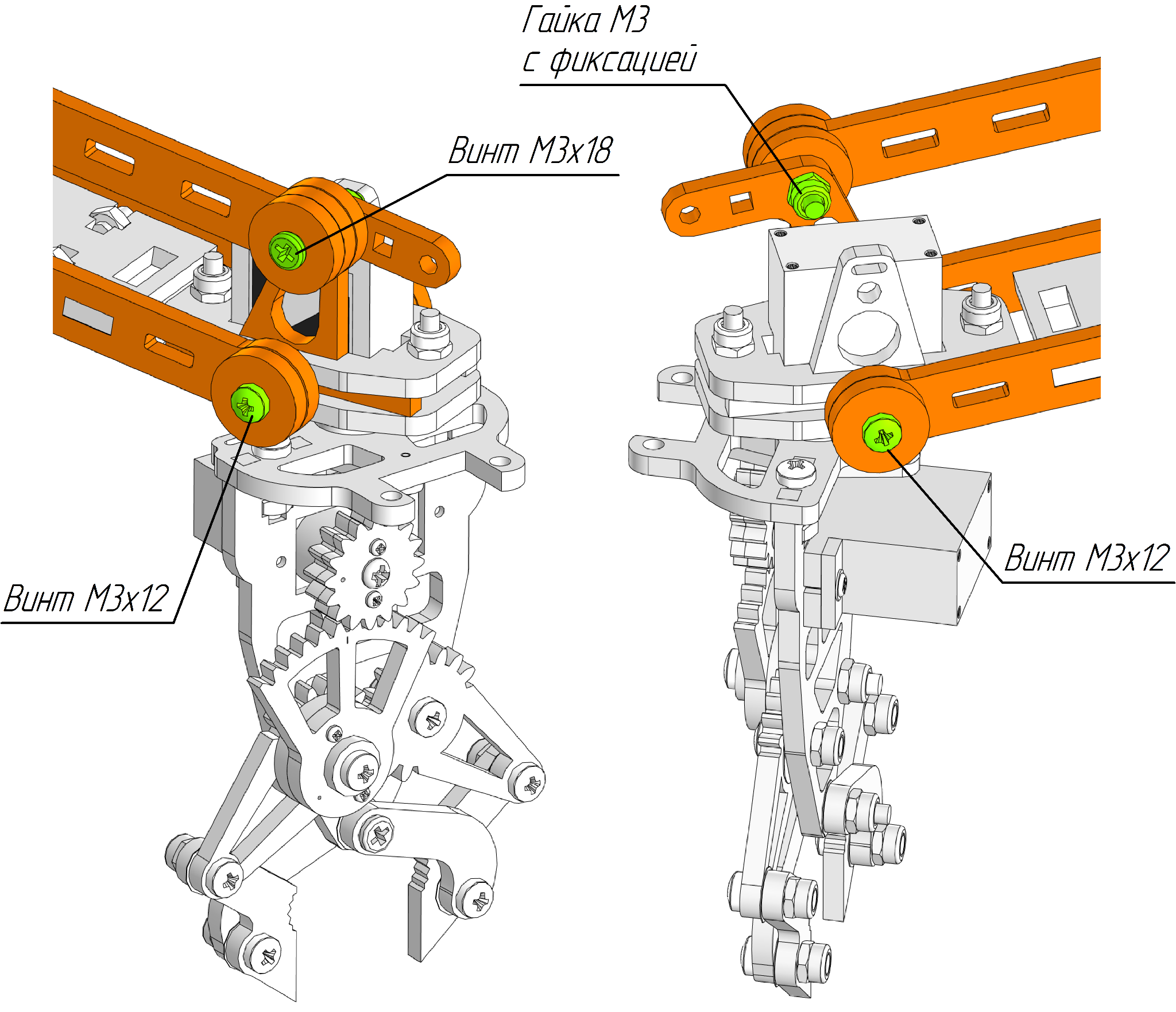
Шаг 2.
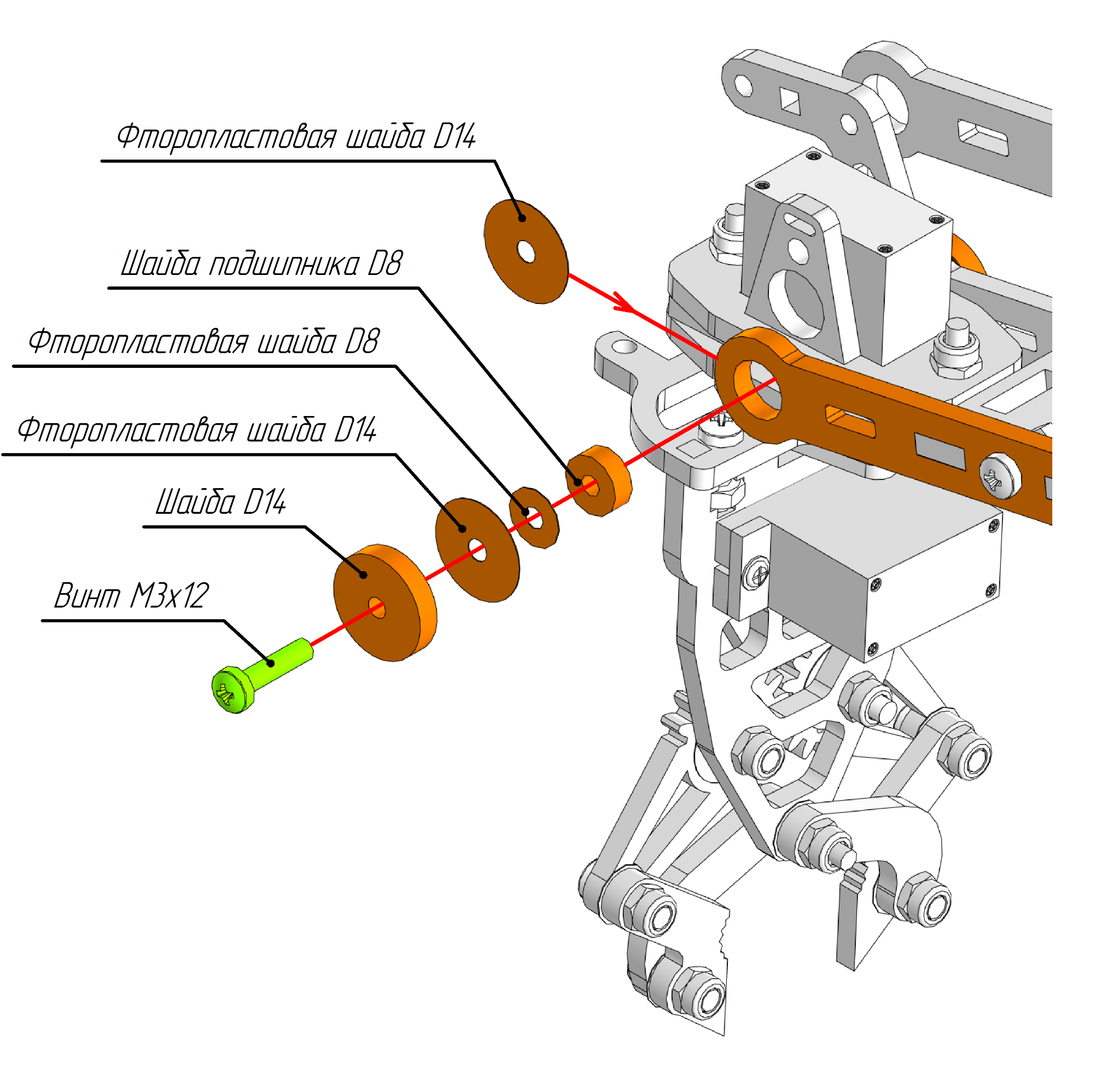
Шаг 3.
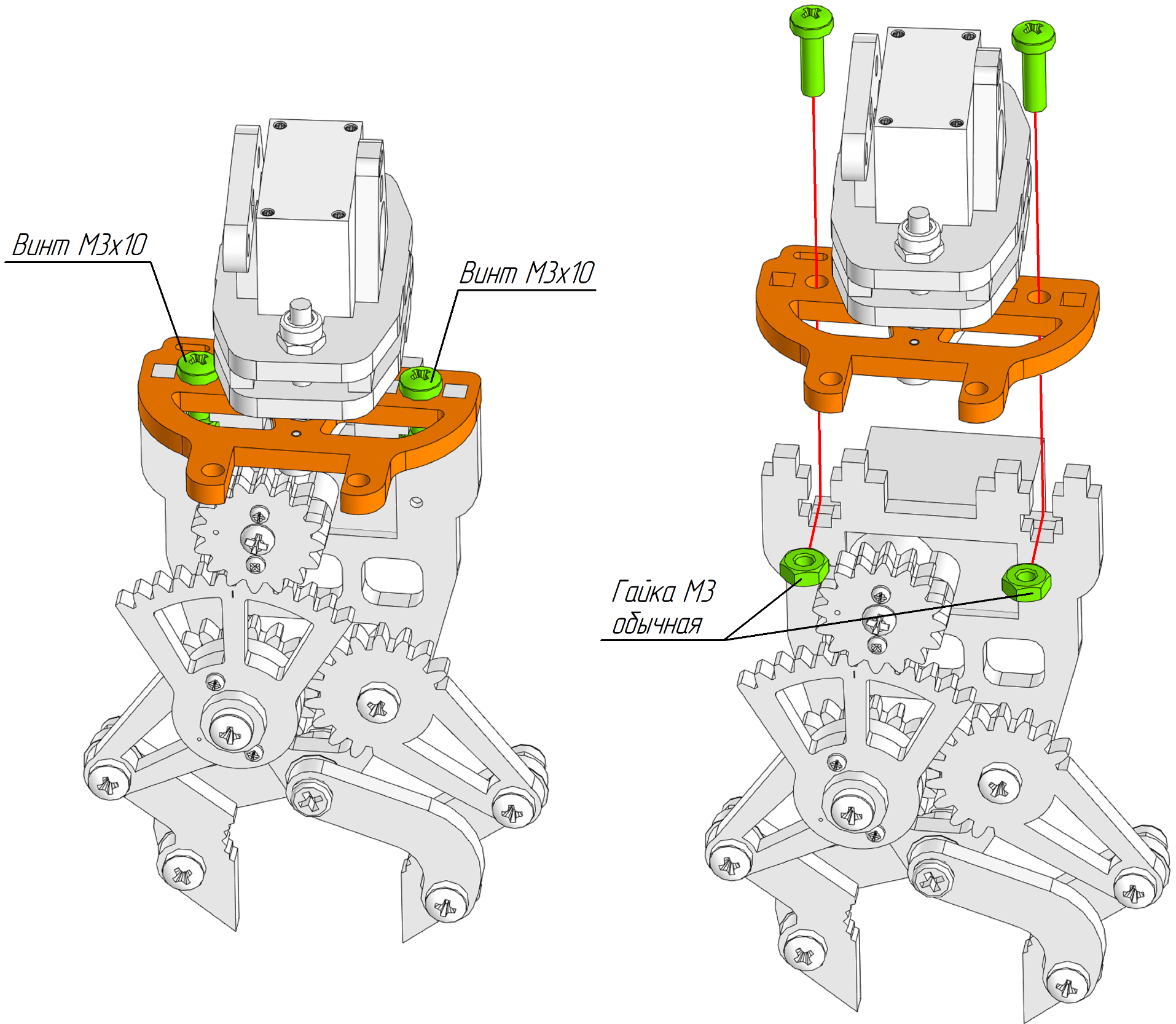
Шаг 4.
Открутите при помощи крестовой отвертки винт М2.5х6 удерживающий планку крепления рамы захвата и снимите ее с вала сервопривода.
Шаг 5.
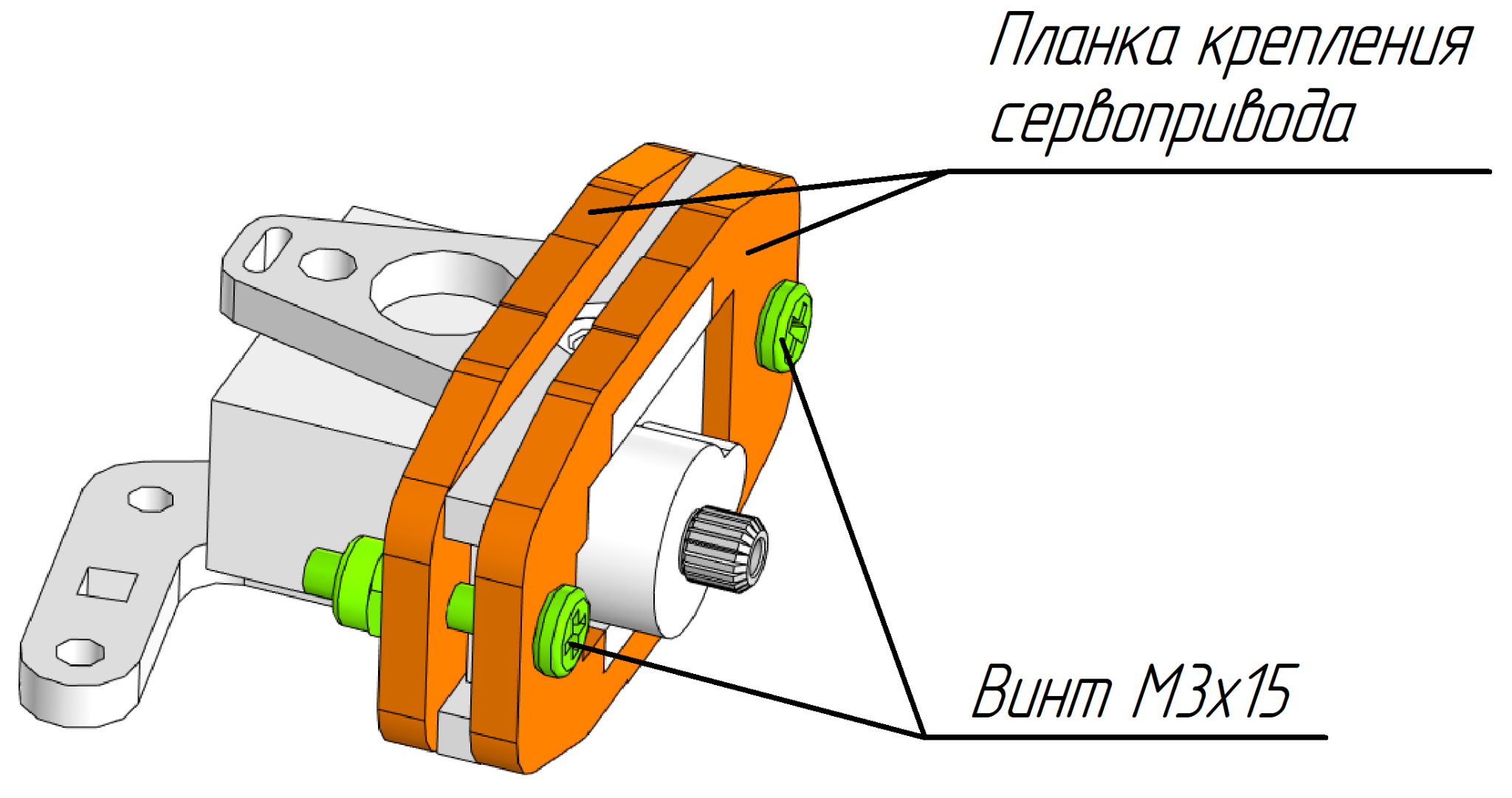
Шаг 6.
Достаньте из ложемента новый исправный сервопривод и установите его, соблюдая ту же последовательность действий, как на предыдущем шаге 5.
Шаг 7.
При помощи программы “Пульт управления РТУ” установите сервопривод в среднее положение. Как установить сервопривод в среднее положение описано в разделе Позиционирование сервоприводов.
Шаг 8.
Не отключая питание робота, не закрывая окно программы «Пульт управления РТУ» и не закрывая окно выставки в среднее положение - установите планку крепления рамы захвата на вал сервопривода как показано в шаге 4. Закрутите винт М2.5х6 удерживающий планку крепления рамы захвата при помощи крестовой отвертки, слегка затяните (во время затяжки придерживайте планку не давая ей вращать вал сервопривода).
Шаг 9.
Соберите захват как показано на шагах 3, 2 и 1 в обратном порядке.
Замена сломанных акриловых рычагов и тяг робота-манипулятора
В процессе эксплуатации робота-манипулятора возможны поломки акриловых деталей. Это возможно, например, при применении излишних физических усилий к рычагам робота, неаккуратной эксплуатации робота, приведшей к падению его с рабочего стола.
Для замены сломанных рычагов в набор входит специальный ремонтный комплект, с помощью которого Вы можете самостоятельно заменить сломанную деталь.
Обращаем Ваше внимание, что узлы креплений рычагов и тяг робота-манипулятора собраны с использованием подшипников скольжения. Подшипники скольжения обеспечивают снижение трения в узлах робота, позволяют свободно и без задержек двигаться рычагам робота, что повышает точность его движений и продляет срок службы. Перед заменой сломанных деталей обязательно изучите раздел настоящего руководства “Описание конструкции и особенности монтажа шарнирных узлов робота с подшипниками скольжения и узла поворотного механизма башни робота”. В данном разделе кратко изложены принципы конструкции и работы подшипников скольжения, а также рекомендации по их сборке и эксплуатации. Тщательное следование рекомендациям позволит Вашему роботу работать точно, без ошибок и поломок.
Для замены открутите сломанную деталь при помощи отверток и гаечного ключа, входящих в комлект набора (или любых аналогичных). Установите аналогичную новую деталь из ремонтного набора (Плата “А” и Плата “Б”). При сборке подшипников, как было упомянуто выше, обязательно следует руководствоваться разделами “Подшипники скольжения и их устройство” и “Описание конструкции и особенности монтажа шарнирных узлов робота с подшипниками скольжения и узла поворотного механизма башни робота” настоящего руководства.
Подшипники скольжения и их устройство
Робот-манипулятор “РобоИнтеллект” модели RM002 имеет несколько подвижных узлов. Это:
- башня манипулятора, которая может вращаться вправо и влево в продольной оси робота;
- манипулятор, рычаги которого позволяют ему подниматься вверх и опускаться вниз, а также перемещаться вперёд-назад;
- клешня, которая сжимается, чтобы захватить груз и разжимается, чтобы освободить груз.
Для того чтобы робот работал надёжно, без сбоев и ошибок, необходимо, чтобы все движения робота были плавными свободными без каких-либо рывков и заеданий. Затруднения в работе данных узлов могут привести к перегреву и выходу из строя сервоприводов робота. Для обеспечения свободного движения в основных узлах робота применяются подшипники скольжения. Подшипник скольжения имеет некоторые особенности реализации, которые необходимо понимать при сборке и настройке узлов робота. Подробно устройство, принципы работы и основные особенности использования подшипников скольжения в роботе-манипуляторе “РобоИнтеллект” модели RM002 приведены ниже в разделе “Описание конструкции и особенности монтажа шарнирных узлов робота с подшипниками скольжения и узла поворотного механизма башни робота”.
Обращаем Ваше внимание! Перед тем, как осуществлять разборку/сборку узлов робота, которые содержат подшипники скольжения обязательно ознакомьтесь с данным разделом. Это позволит Вам успешно заменить сломанные детали робота и обеспечит долгую и бесперебойную его работу впоследствии.
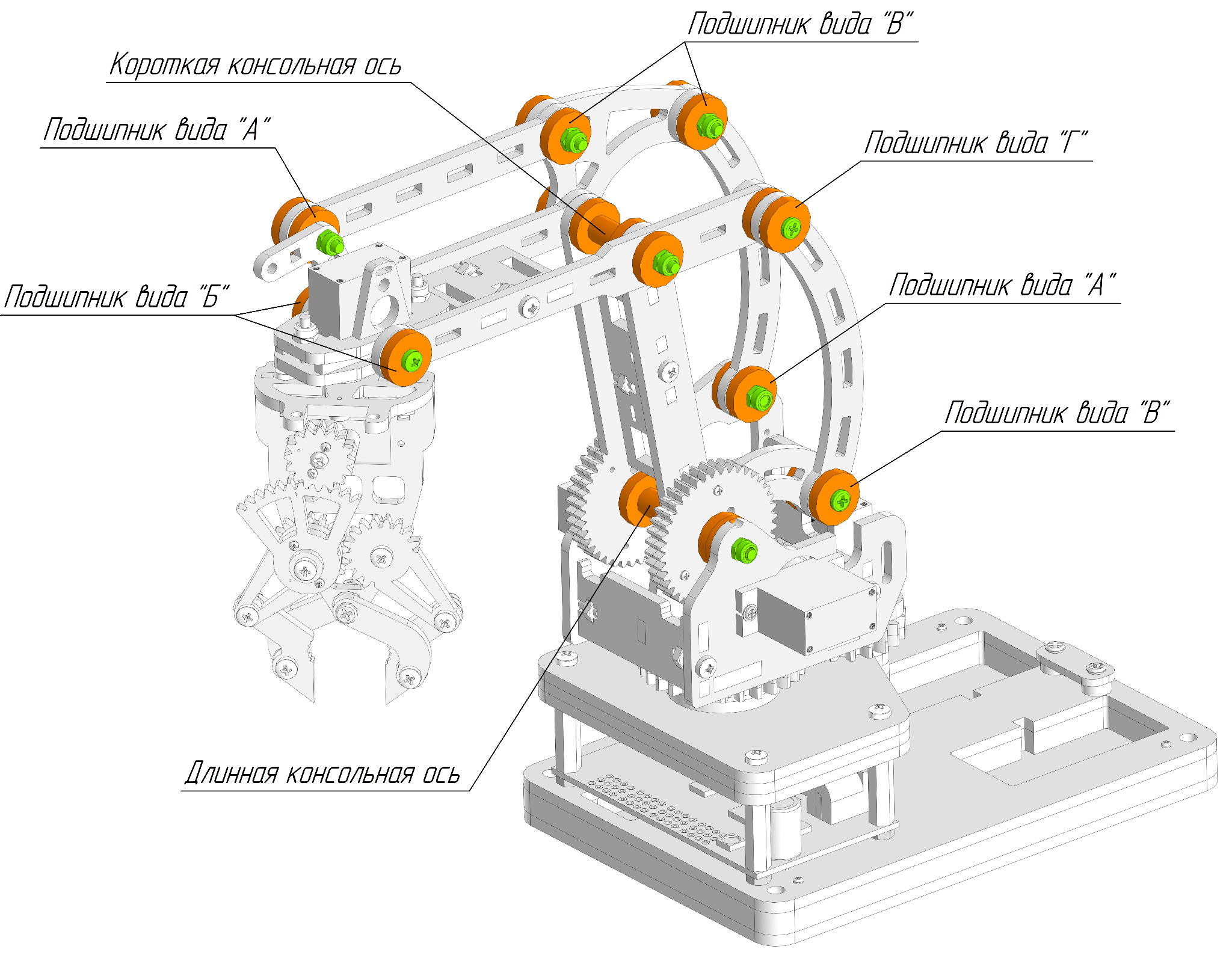
Устройство подшипника вида “А”
Устройство подшипника вида “Б”
Устройство подшипника вида “В”
Устройство подшипника вида “Г”
Устройство короткой консольной оси
Для того чтобы разобрать и собрать короткую консольную ось, необходимо при помощи крестовой отвертки открутить два винта М3х10. А также, при помощи крестовой отвертки и гаечного ключа открутить гайку с фиксатором.
Ниже представлено подробное устройство короткой консольной оси. Сборку короткой консольной оси проводить в обратном порядке.
Устройство длинной консольной оси
Чтобы разобрать и собрать длинную консольную ось Вам предстоит выполнить несколько шагов.
Шаг 1.
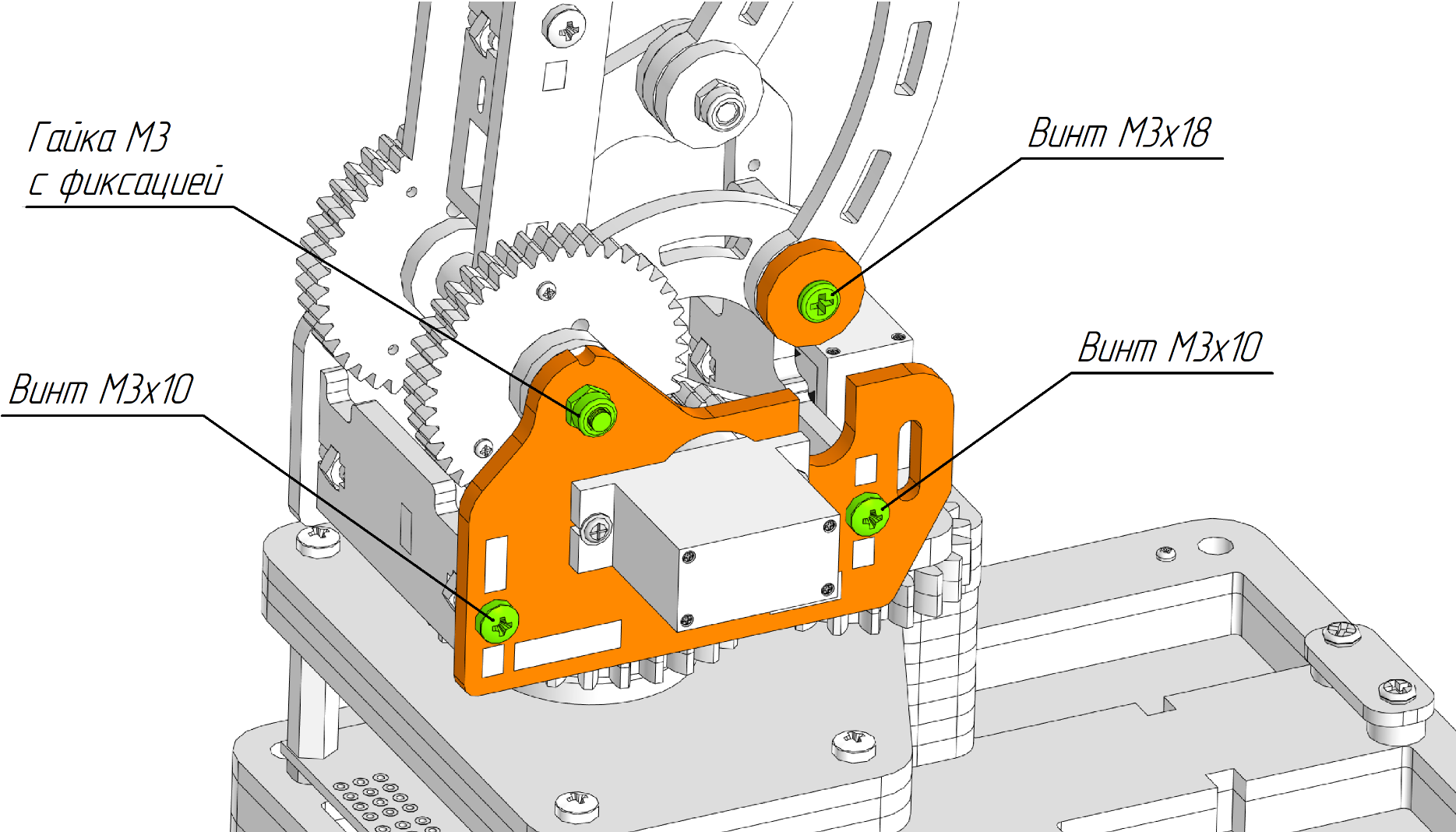
Шаг 2.
Аккуратно снимите боковую стенку основания башни вместе с сервоприводом и отложите ее в сторону. Снимите шестерню рычаг и также отложите ее в сторону.
Ниже представлено подробное устройство короткой консольной оси. Сборку длинной консольной оси проводить в обратном порядке.
Описание конструкции и особенности монтажа шарнирных узлов робота с подшипниками скольжения и узла поворотного механизма башни робота
Представленный робот-манипулятор RM002 имеет несколько подвижных узлов. Это:
- башня манипулятора, которая может вращаться вправо и влево в продольной оси робота;
- манипулятор, рычаги которого позволяют ему подниматься вверх и опускаться вниз, а также перемещаться вперёд-назад;
- клешня, которая сжимается, чтобы захватить груз и разжимается, чтобы освободить груз.
Для того чтобы робот работал надёжно, без сбоев и ошибок, необходимо, чтобы все движения робота были плавными свободными без каких-либо рывков и заеданий. Затруднения в работе данных узлов могут привести к перегреву и выходу из строя сервоприводов робота. Для обеспечения свободного движения в основных узлах робота применяются подшипники скольжения. Подшипник скольжения имеет некоторые особенности реализации, которые необходимо понимать при сборке и настройке узлов робота.
В наборе робота-манипулятора RM002 подшипник скольжения обеспечивает необходимые зазоры между подвижной и неподвижными деталями в узлах робота и выглядит как круглая шайба. Поэтому, для простоты обозначений, в наборе подшипник скольжения называется “шайба-подшипник”. Шайбы-подшипники - подшипники скольжения используются в следующих узлах:
- крепления зубчатого привода клешни позволяет приводу клешни свободно вращаться на своей оси (шайба-подшипник D8x3 диаметром 8 мм);
- крепления левой планки рычага и поворотной шестерни с дугой на оси обеспечивают свободное движение манипулятора робота вверх-вниз;
- крепления правой планки-шестерни нижнего плеча на оси обеспечивает свободное движение манипулятора робота вперёд-назад;
- крепления рычагов левой стороны манипулятора обеспечивают свободное движение манипулятора робота вперёд-назад;
- крепления сервопривода привода башни на основание робота обеспечивает свободное движение башни манипулятора вправо-влево;
- крепления клешни к рычагам манипулятора обеспечивают свободное движение клешни относительно рычагов манипулятора при их движении.
Разберёмся в принципе работы подшипника скольжения более подробно. Подшипник скольжения - шайба-подшипник создаёт необходимые
Зазор А и Зазор Б между подвижной и неподвижными деталями узлов робота для уменьшения силы трения между ними. На рисунке ниже схематически показан такой узел.Схематичное изображение конструкции и принципа работы подшипника скольжения с шайбой-подшипником D8, используемого в шарнирах рычагов манипулятора робота
Схематичное изображение конструкции и принципа работы подшипника скольжения с шайбой-подшипником D22, используемого в креплении башни манипулятора к основанию робота
Шайба-подшипник создаёт Зазор А между подвижной деталью и её опорой в узле робота и Зазор Б между осью вращения и подвижной деталью. Дополнительно для уменьшения трения между подвижной деталью и её опорой применяются большие фторопластовые шайбы (как известно, материал фторопласт имеет один из самых низких коэффициентов трения) D14 для узлов с шайбами-подшипниками диаметра 8 мм и D22 для узла крепления сервопривода башни к основанию, где применяетсяшайба-подшипник диаметром 22 мм .Наличие Зазора А и Зазора Б позволяет подвижной и неподвижным деталям минимально соприкасаться друг с другом. В то же время, такие зазоры не должны быть слишком большими, иначе детали будут “болтаться” и при движении могут возникать перекосы деталей, что может привести к их “заклиниванию”. Для любого узла, содержащего подшипник скольжения, минимальный Зазор А должен быть 0,1 мм, максимальный 0,2 мм, оптимальное значение зазора составляет 0,15 мм. В связи с применяемым методом лазерной резки пластика края деталей имеют небольшие утолщения, представляющие собой “наплывы” расплавленного в процессе резки пластика. Именно данные “наплывы” делают желательным формирование Зазора А 0,15 мм.
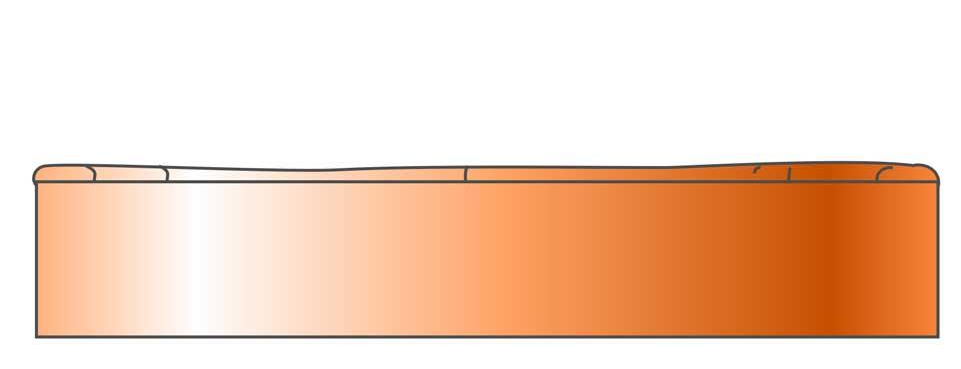
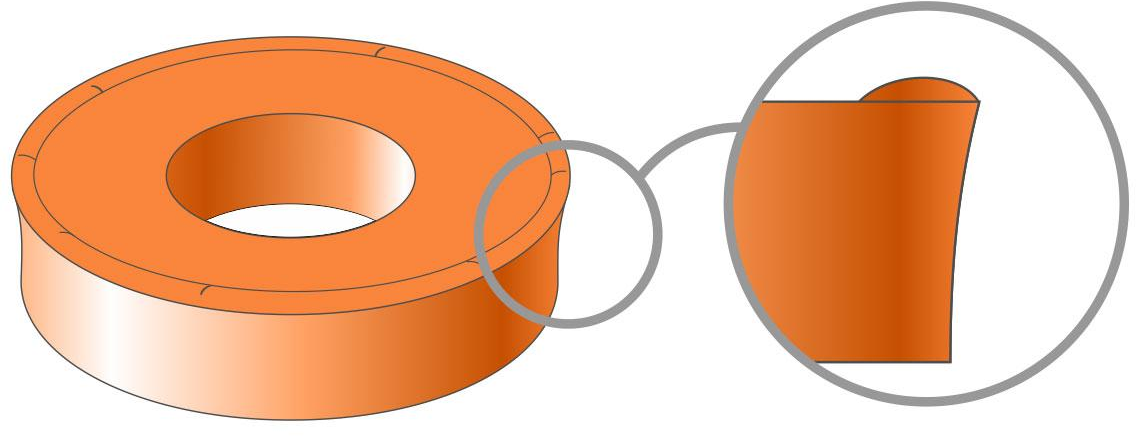
Схематичное изображение “наплыва” пластика в верхней части детали в результате лазерной резки
Если же такие “наплывы” оказываются слишком большими, то необходимо удалить эти “наплывы” надфилем или мелкозернистой наждачной бумагой, как указано в разделе “Важные особенности монтажа узлов, в которых используются шайбы-подшипники!”.
Конструктивно подвижная деталь и Шайба-подшипник должны совпадать по толщине и Зазор А формируется только за счёт фторопластовых шайб - прокладок создания Зазора А. Поскольку на практике часто оказывается, что толщина пластика неравномерна в пределах одного листа пластика из которого изготавливаются детали робота, а разные листы пластика могут значительно отличаться по толщине (в пределах 1 мм). Связано это с особенностями изготовления листов пластика - акрила. Существует две основные технологии изготовления листового акрила - литьевым методом и экструзионным методом. Для литьевого метода разница в толщине акрила для разных листов акрила имеет допуск до 30%, что при толщине листа в 3 мм приводит к тому, что детали изготовленные из разных листов акрила могут отличаться по толщине более чем на 1 мм. Для экструзионной технологии изготовления допуск составляет 5%. В обоих случаях может появляться разница в толщине подвижной детали и Шайбы-подшипника, препятствующая корректной работе подшипника скольжения.
Для коррекции разной толщины подвижной детали и шайбы-подшипника, чтобы обеспечить оптимальный Зазор А, используются дополнительные фторопластовые шайбы-прокладки создания Зазора А: D8 для узлов с шайбами-подшипниками диаметра 8 мм и D22 для узла крепления сервопривода башни к основанию, где применяется шайба-подшипник диаметров 22 мм. Набор специально комплектуется дополнительными шайбами-прокладками в количестве большем, чем необходимо конструктивно. Количество устанавливаемых шайб-прокладок нужно установить самостоятельно, визуально проверяя Зазор А и контролируя свободность хода узла в процессе его сборки. При достижении оптимального зазора в 0,15 мм узел должен вращаться свободно без какого-либо, даже лёгкого, сопротивления и иметь минимальный люфт, практически отсутствующий на ощупь.
Схематичное изображение подшипника скольжения при толщине шайбы-подшипника D8 меньшей, чем толщина подвижной детали и использовании дополнительных фторопластовых шайб для создания оптимального Зазора А
Если же толщина шайбы-подшипника больше толщины подвижной детали, то при сборке узла возможно не использовать ни одной фторопластовой шайбы-прокладки. Это позволит сделать Зазор А оптимальным и избежать излишнего люфта подвижной детали.
Схематичное изображение подшипника скольжения при толщине шайбы-подшипника D8 большей, чем толщина подвижной детали и исключении фторопластовой шайбы для создания оптимального Зазора А
Зазор Б создаётся за счёт конструктивной разницы диаметров внутренней окружности - посадочного отверстия на подвижной детали и внешнего диаметра шайбы-подшипника. Оптимальный размер Зазора Б равен 0,1 мм. Недостаточный размерЗазора Б или его полное отсутствие являются второй важной причиной “заедания” и заклинивания работы подвижных узлов с подшипниками скольжения.Есть две основные причины, которые могут привести к недостаточному Зазору Б. Первая причина - это возможные неровности на торцах деталей, образующих Зазор Б. Такие неровности могут возникать в процессе лазерной резки пластика на торцах деталей и выглядят как очень маленькие заусенцы. Наличие заусенцев можно увидеть внимательно посмотрев на торцы деталей или проведя по торцам деталей пальцем.
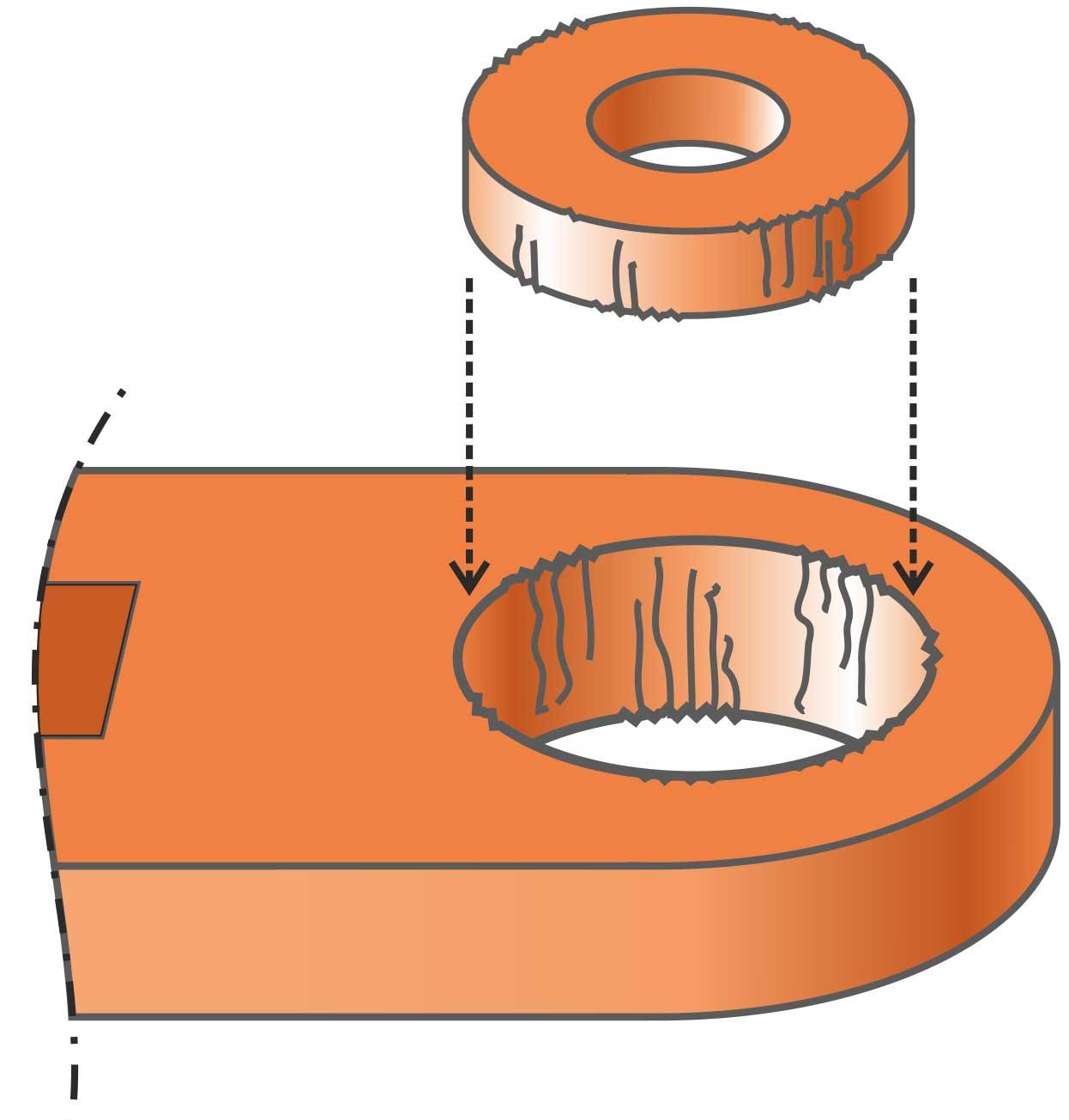
Второй причиной является наклон или “конусность” торцов деталей от вертикали. Такая конусность возникает потому, что лазерный луч, который формируется станком для лазерной резки, расширяется или, как говорят, расфокусируется на определённом расстоянии от фокусирующей линзы. Границы лазерного луча становятся не параллельными друг другу, а расходящимися. Это физический эффект распространения лазерного луча в пространстве. Несмотря на малые расстояния от фокусирующей линзы лазерного станка до пластика, из которого вырезаны детали Вашего набора, лазерный луч успевает расфокусироваться на доли градуса, но этого достаточно, чтобы торец вырезаемой детали имел небольшой наклон или конусность. Поскольку при изготовлении деталей наши инженеры постоянно проверяют настройки фокусировки лазерного станка, такая конусность примерно одинакова на торцах всех деталей.
При сборке узлов с шайбами-подшипниками обязательно необходимо учитывать такую конусность и собирать подвижную деталь и шайбу-подшипник таким образом, чтобы наклон внутреннего торца посадочного отверстия был направлен в другую сторону от наклона торца шайбы-подшипника. Т. е. торцы деталей должны быть параллельны друг другу. Тогда Зазор Б будет ровным на всей толщине собираемого узла.
Подробно об учёте конусности деталей при сборке узлов, содержащих шайбу-подшипник, изложено ниже в разделе “Учёт угла наклона (конусности) торца посадочного отверстия подвижной детали и внешнего торца шайбы-подшипника”
Понимание конструкции, основ работы подшипников скольжения, а также особенностей практической реализации в каждом конкретном случае позволит грамотно выполнить процесс сборки и добиться свободного хода всех подвижных узлов, содержащих подшипники скольжения.
Свободный ход обеспечивается без применения каких-либо смазочных материалов, но для улучшения работы подвижных узлов рекомендуется применить силиконовую смазку для Зазора А и Зазора Б, как показано на рисунке ниже.
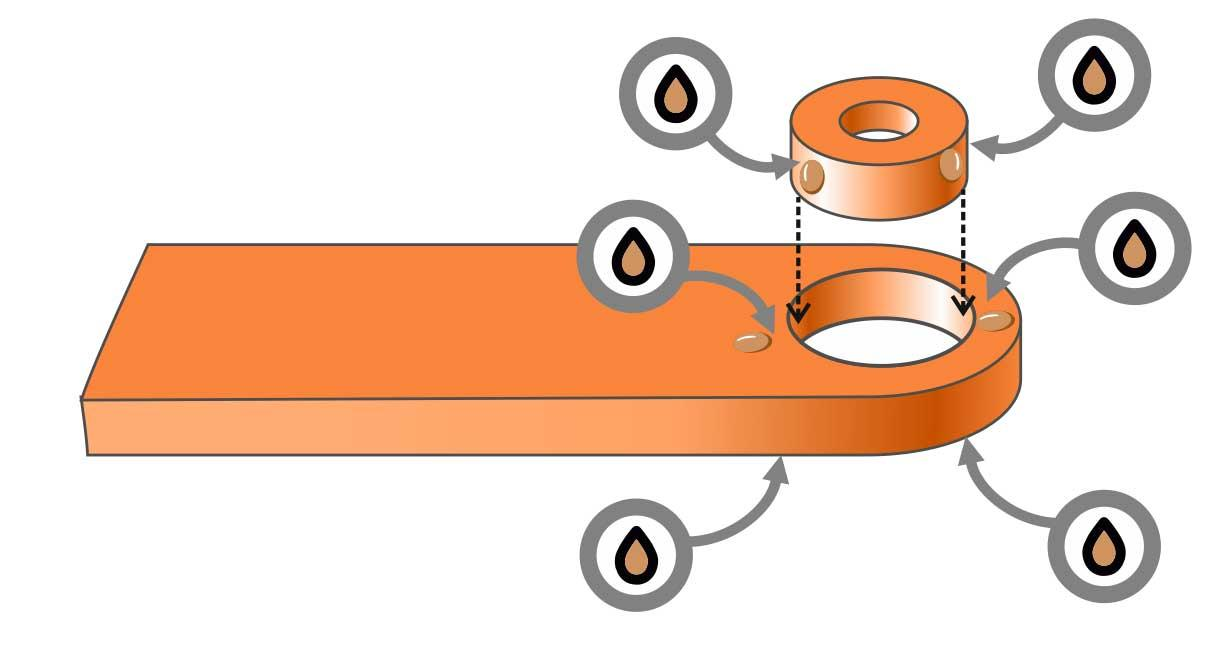

На рисунке схематично показаны места смазки силиконовой смазкой в узлах, содержащих подшипники скольжения
Для детального понимания работы подшипников скольжения в роботе на рисунках ниже приведены примеры чертежей двух узлов содержащих шайбу-подшипник.
На рисунке изображён пример сборки узла крепления рычага манипулятора робота, где применяется шайба-подшипник диаметром 8 мм
На рисунке изображён пример сборки узла крепления сервопривода башни к основанию, где применяется шайба-подшипник диаметром 22 мм
Важные особенности монтажа узлов, в которых используются шайбы-подшипники!
Учёт угла наклона (конусности) торца посадочного отверстия подвижной детали и внешнего торца шайбы-подшипника
Аналогично сборке шестерёнчатых редукторов, при установке шайб-подшипников в соответствующие отверстия рычагов обязательно учитывайте угол наклона (“конусность”) торцов деталей. Всегда устанавливайте шайбу-подшипник так, чтобы “конусности” торцов шайбы-подшипника и соответствующего отверстия рычага были направлены в одну сторону. При этом шайба-подшипник устанавливается плоскостью с меньшим диаметром в отверстие рычага с той стороны, где диаметр отверстия рычага больше. Таким образом обеспечивается равномерность зазора “b”.
Ровность торца посадочного отверстия подвижной детали и внешнего торца шайбы-подшипника
Ровность торцов деталей также влияет на равномерность Зазора Б между подвижной и неподвижной деталями узла. Детали робота изготавливаются путем вырезания из листа пластика на станке для лазерной резки. Лазерная резка позволяет обеспечить необходимую ровность и гладкость торца деталей. Однако перед сборкой узла рекомендуется проверить это.
Внимательно осмотрите внутренний торец посадочного отверстия в подвижной детали и внешний торец шайбы-подшипника. Можно провести по ним пальцем. Поверхность торцов деталей должна быть ровной без заусенцев. Допускаются небольшие вертикальные канавки на торцах деталей - это следы лазерной резки и они не препятствуют движению деталей. Если же будут выявлены заусенцы, необходимо надфилем или мелкозернистой наждачной бумагой удалить заусенцы на торцах деталей.
Затем, не собирая узел, необходимо проверить лёгкость движения шайбы-подшипника в посадочном отверстии подвижной детали. Для этого перед сборкой узла вставьте шайбу-подшипник в соответствующее посадочное отверстие и пальцами покрутите подвижной деталь вокруг шайбы-подшипника. Движение должно быть свободным ровным. Если заметны какие-либо заедания или рывки, необходимо ещё немного отшлифовать торцы деталей.
После шлифовки деталей обязательно необходимо очистить их от стружек и пыли, которые возникают при обработке деталей надфилем или наждачной бумагой. Очистить детали можно мягкой кистью или, при её отсутствии, подув на обработанные детали.
Свободное ровное вращение шайбы-подшипника в посадочном отверстии позволит собираемому Вами роботу работать надёжно, без ошибок и сбоев.
Удаление “наплывов” пластика на деталях
В связи с применяемым методом лазерной резки пластика края деталей могут иметь небольшие утолщения, представляющие собой “наплывы” расплавленного в процессе резки пластика.
Такие “наплывы” можно увидеть, посмотрев на поверхность пластиковых деталей набора или проведя пальцев по верхней и нижней поверхностям деталей в местах реза. Как правило, размер таких “наплывов” крайне мал и никак не влияет на работу узлов робота.
Однако в случае неоднородности структуры пластика, которая может возникать при его литье, такие “наплывы” могут быть достаточно большими, чтобы помешать работе подвижных узлов. “Наплывы” приводят к тому, что Зазор А становиться неравномерный, детали могут цепляться друг за друга или цепляться за поверхность прилегающей сверху или снизу детали.
Если такие “наплывы” будут, их обязательно необходимо удалить надфилем или мелкозернистой наждачной бумагой. Для этого можно положить надфиль или лист наждачной бумаги на ровную поверхность, например стол, прижав их одной рукой так, чтобы они были неподвижными, и другой рукой круговыми движениями отшлифовать места реза на нижней и верхней стороне деталей.
После обработки деталей обязательно необходимо очистить их от стружек и пыли, которые возникают при обработке деталей надфилем или наждачной бумагой. Очистить детали можно мягкой кистью или, при её отсутствии, подув на обработанные детали.
Контроль одинаковой толщины подвижной детали и шайбы-подшипника
Как было упомянуто выше, для ровного и свободного движения деталей в узле с шайбой-подшипником требуется равномерный Зазор А между подвижной деталью и её опорой.
Данный зазор достигается избыточной толщиной шайбы-подшипника, т. е. толщина шайбы-подшипника должны быть немного больше толщины подвижной детали. Тогда подвижная деталь имеет свободный ход между своей опорой сверху и снизу и может свободно вращаться.
Поскольку используемый для изготовления деталей набора пластик может иметь немного разную толщину по площади листа, обусловленную погрешностями оборудования при его изготовлении, перед сборкой узла, содержащего шайбу-подшипник, обязательно нужно проверить отличается ли толщина шайбы-подшипника от толщины подвижной детали.
Для этого положите шайбу-подшипник и подвижную деталь на ровную плоскую поверхность, например на стол, рядом друг с другом и визуально сравните их толщину.
Если толщина обеих деталей одинакова, для создания необходимого Зазора А обязательно используйте дополнительную фторопластовую шайбу D8 создания Зазора А для узлов с шайбами-подшипниками диаметра 8 мм.
Если толщина шайбы-подшипника больше толщины подвижной детали, то при сборке узла возможно не использовать дополнительную фторопластовую шайбу. Это позволит не сделать Зазор А слишком большим и избежать излишнего люфта подвижной детали.
Если толщина шайбы подшипника меньше толщины подвижной детали, используйте несколько дополнительных фторопластовых шайб, установив их одну на другую. Запасные шайбы есть в наборе.
Наличие достаточного и равномерного Зазора А позволит узлу двигаться ровно и свободно и сохранить работоспособность сервоприводов в Вашем роботе.